LVL (Laminated Veneer Lumber) construction materials have gained popularity in the building industry due to their excellent structural characteristics and enhanced durability. Understanding the composition, manufacturing process, and properties of LVL is crucial to comprehend how these materials contribute to the overall structural integrity of buildings. This article delves into the significance of LVL materials and compares them with traditional construction materials, explores their environmental impact, and highlights upcoming trends in LVL manufacturing.
Understanding LVL Construction Materials
LVL materials are engineered wood products made by bonding thin layers of wood veneers together. This composition enhances their strength and durability, making them an ideal replacement for traditional solid wood beams in construction projects. The manufacturing process of LVL materials involves several stages, ensuring their consistency and reliability.
LVL materials have gained popularity in the lvl construction industry due to their versatility and sustainability. The use of fast-growing trees for the production of veneers reduces the demand for slow-growing hardwoods, promoting responsible forestry practices. Additionally, the engineered nature of LVL materials allows for longer spans and higher load-bearing capacities, providing architects and builders with more design flexibility.
Definition and Composition of LVL Materials
Laminated Veneer Lumber (LVL) is a type of engineered wood made from layers of thin wood veneers. These veneers are usually obtained from fast-growing trees such as pine or poplar, making LVL a sustainable alternative to solid wood. The veneers are stacked together and bonded with strong adhesives, creating a composite material that exhibits superior strength and stability.
Furthermore, the manufacturing process of LVL materials results in a more uniform and predictable product compared to natural wood. The controlled environment in which LVL is produced ensures consistent quality and performance, reducing waste and optimizing resource utilization. This reliability makes LVL an attractive choice for structural applications where precision and strength are paramount.
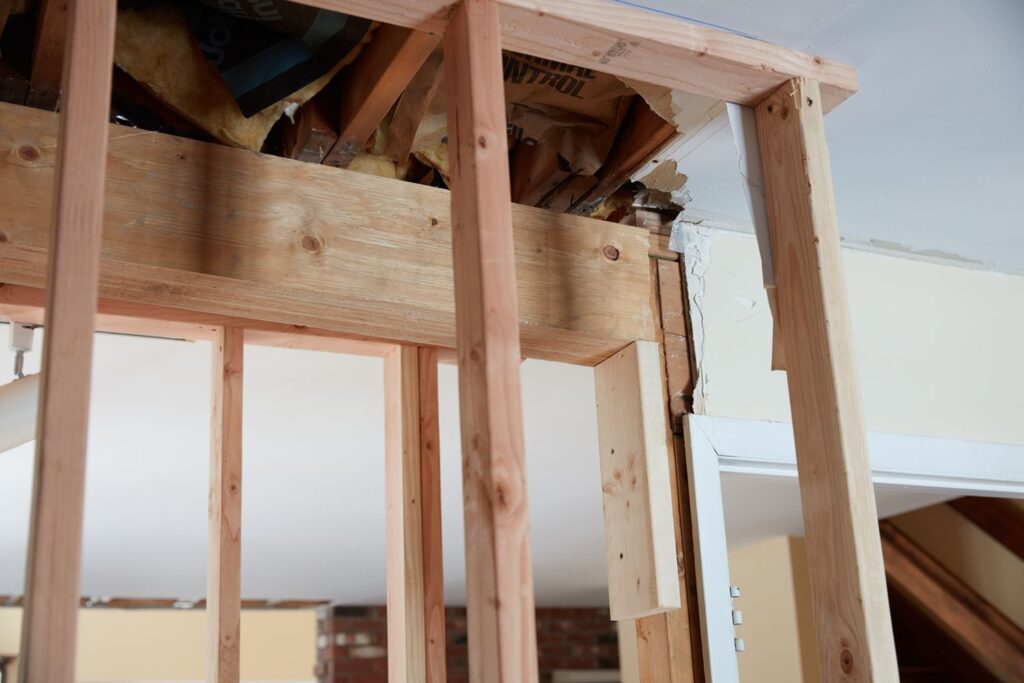
The Manufacturing Process of LVL Materials
The production of LVL materials begins with carefully selecting and peeling logs to obtain thin veneers. These veneers are then dried and graded for quality control. Next, the veneers are arranged in a parallel pattern and bonded together with adhesives. This assembly is subjected to heat and pressure to create a strong and homogeneous LVL panel. Once the panels are formed, they are cut into desired sizes and treated to protect against moisture and fungal attacks.
Throughout the manufacturing process, stringent quality control measures are implemented to ensure that each LVL panel meets industry standards for strength, durability, and dimensional stability. By adhering to strict production guidelines, manufacturers can guarantee the performance and longevity of LVL materials in various construction applications. This commitment to excellence has solidified LVL’s reputation as a reliable and cost-effective building material in the modern construction landscape.
The Role of LVL Materials in Structural Integrity
LVL (Laminated Veneer Lumber) materials are a critical component in enhancing the structural integrity of buildings. Their exceptional strength and durability make them a popular choice for various construction applications, such as beams, headers, and joists. Beyond their basic functionality, LVL materials offer a range of benefits that contribute to the overall stability and longevity of structures.
One significant advantage of LVL materials is their eco-friendliness. Made from sustainable wood sources, LVL production minimizes environmental impact while providing a reliable and robust building material. This sustainable aspect aligns with modern construction practices that prioritize green building and sustainable design.
Key Properties of LVL Materials
LVL materials exhibit a combination of key properties that make them highly suitable for structural applications. These properties include a remarkable strength-to-weight ratio, exceptional dimensional stability, and resistance to common issues like warping and splitting. By incorporating these properties, LVL materials offer a reliable solution for architects and builders seeking long-term structural performance with minimal maintenance requirements.
Moreover, the manufacturing process of LVL materials involves precise engineering and quality control measures to ensure consistency and reliability across each panel. This meticulous approach results in uniformity in strength and performance, making LVL materials a dependable choice for critical load-bearing components in construction projects.
How LVL Materials Contribute to Structural Strength
The innovative design of LVL materials plays a crucial role in enhancing structural strength within buildings. By strategically arranging thin veneers in a cross-laminated pattern, LVL panels can effectively distribute any natural defects present in the wood. This distribution minimizes the impact of individual imperfections on the overall structural integrity, providing a more resilient and predictable material for construction purposes.
Furthermore, the superior load-carrying capacity of LVL materials enables them to withstand heavy loads and support larger spans compared to traditional lumber. This increased load-bearing capability expands the design possibilities for architects and engineers, allowing for more open and spacious interior layouts in buildings without compromising on structural stability.
Comparing LVL Materials with Traditional Construction Materials
When compared to traditional construction materials such as solid wood and steel, LVL materials offer unique advantages and present viable alternatives for builders and architects.
Engineered wood products like LVL (Laminated Veneer Lumber) have gained popularity in the construction industry due to their exceptional strength and versatility. LVL materials are created by bonding multiple layers of wood veneers together with adhesives, resulting in a composite material that surpasses the natural limitations of solid wood. This manufacturing process allows for precise customization of dimensions and properties, making LVL an ideal choice for a wide range of structural applications. Learn more about solid on https://www.chem.purdue.edu/gchelp/liquids/character.html
LVL vs. Solid Wood: A Comparative Analysis
LVL materials have a distinct edge over solid wood in terms of consistency and performance. While solid wood beams may contain natural defects, knots, and uneven grain patterns that can weaken their structural integrity, LVL materials exhibit uniform strength due to their engineered composition. Moreover, LVL materials are less prone to shrinking, warping, or splitting that can occur in solid wood over time.
Furthermore, LVL materials offer enhanced load-carrying capacity and dimensional stability, making them particularly suitable for long-span structures and high-load applications. The predictable strength and durability of LVL components contribute to more efficient construction practices and longer-lasting buildings.
LVL vs. Steel: Strengths and Weaknesses
When it comes to comparing LVL with steel, both materials have their strengths and weaknesses. LVL materials offer a more cost-effective solution while providing comparable strength. Additionally, LVL materials are easier to work with, lightweight, and more resistant to thermal and electrical conductivity compared to steel. However, steel may be preferred in certain applications where high tensile strength or fire resistance are crucial factors.
Despite the competition from steel, LVL materials continue to gain traction in the construction industry for their sustainability and environmental benefits. LVL is often sourced from fast-growing plantation trees, making it a renewable resource that promotes responsible forestry practices. The energy-efficient production process of LVL further contributes to reducing the carbon footprint associated with building materials, aligning with the growing emphasis on green construction practices.
The Environmental Impact of Using LVL Materials
In today’s construction industry, sustainability and environmental impact are key considerations. LVL materials offer several advantages from an environmental standpoint.
Sustainability of LVL Materials
LVL materials are manufactured from fast-growing trees, ensuring a renewable source of raw material. By utilizing LVL instead of solid wood, forests can be preserved and managed more sustainably. Furthermore, LVL manufacturing processes have become more efficient, reducing waste and energy consumption in production.
Moreover, the use of LVL materials can also help in reducing deforestation rates. By promoting the use of fast-growing trees in construction, the demand for old-growth forests decreases, leading to the preservation of these valuable ecosystems. This shift towards sustainable forestry practices not only benefits the environment but also supports biodiversity and wildlife habitats.
LVL Materials and Carbon Footprint
Compared to other construction materials, LVL materials have a relatively low carbon footprint. The production of LVL requires fewer fossil fuel-intensive processes compared to steel or concrete. Additionally, LVL’s lightweight nature contributes to more efficient transportation and reduced fuel consumption during delivery to construction sites.
Furthermore, the longevity of LVL materials should be considered when evaluating their environmental impact. LVL products are known for their durability and resistance to warping, shrinking, and splitting, which means they have a longer lifespan than some traditional building materials. This extended lifespan reduces the need for frequent replacements and repairs, ultimately decreasing the overall environmental impact associated with construction and maintenance activities.
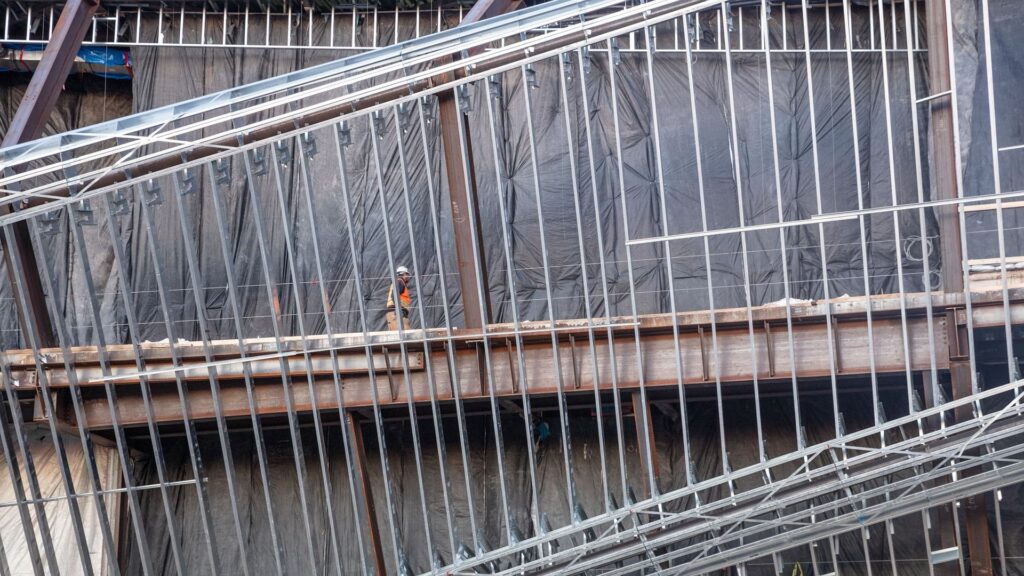
Future Trends in LVL Construction Materials
As technology continues to advance, the manufacturing of LVL materials is expected to undergo further improvements, leading to new trends and innovations in the construction industry.
One of the key areas of focus in LVL manufacturing is the development of modified adhesives. These adhesives are designed to enhance the bonding strength between the veneer layers, resulting in LVL materials with even greater structural integrity. By improving the bonding techniques, manufacturers can ensure that LVL products can withstand higher loads and provide increased stability for a wide range of construction applications.
In addition to modified adhesives, researchers are also exploring alternative fiber sources for LVL production. Traditionally, LVL materials are made from softwood veneers, but advancements in technology have opened up possibilities for using other types of fibers. For example, bamboo, a fast-growing and sustainable resource, has shown great potential as a viable alternative to traditional wood fibers. By incorporating bamboo fibers into LVL manufacturing, builders can further reduce the environmental impact of construction while maintaining the strength and durability of the materials. To find more about durability click here.
The Growing Demand for LVL in Modern Construction
The demand for LVL materials in modern construction continues to rise due to their numerous benefits. Architects and builders recognize the advantages of using LVL in structural applications, including its predictable performance, cost-effectiveness, and sustainable characteristics.
One of the key advantages of LVL materials is their predictable performance. Unlike solid wood, LVL products have consistent strength and dimensional stability, making them ideal for applications where structural integrity is crucial. This predictability allows architects and engineers to design with confidence, knowing that the LVL materials will meet the required specifications and deliver reliable performance.
Cost-effectiveness is another factor driving the demand for LVL in construction. While LVL materials may have a higher upfront cost compared to traditional lumber, their superior strength and durability can result in long-term savings. LVL products require less maintenance and have a longer lifespan, reducing the need for frequent replacements and repairs.
Furthermore, as green building practices become more prevalent, LVL materials are expected to play a vital role in meeting environmental goals without compromising structural integrity. LVL is a sustainable choice for construction as it is made from renewable resources and can be recycled at the end of its life. By incorporating LVL into their projects, builders can contribute to reducing the carbon footprint of the construction industry and create more sustainable structures for future generations.
In conclusion, LVL construction materials significantly enhance the structural integrity of buildings. Their unique composition, manufacturing process, and properties make them a reliable and environmentally friendly choice for various construction applications. Additionally, the ongoing advancements in LVL manufacturing and the growing demand for sustainable building practices indicate a promising future for these versatile materials.
Read about lvl beams on: Exploring the Strength and Durability of LVL Beams in Formwork
Leave a Reply