Laminated Veneer Lumber (LVL) beams are a crucial component in modern construction, particularly in formwork systems. They provide structural support and stability, ensuring the safety and durability of various construction projects. In this article, we will delve into the factors that contribute to the strength and longevity of LVL beams, as well as the advancements and innovations being made in the field of LVL beam production.
Understanding LVL Beams
Definition and Characteristics of LVL Beams
LVL beams are engineered wood products made by bonding multiple layers of thin wood veneers together with adhesives. This construction method results in a high-strength beam that offers superior load-bearing capabilities compared to traditional solid wood or steel beams. The adhesive used in LVL beam production ensures consistent quality and structural integrity throughout the beam’s length.
One of the key characteristics of LVL beams is their dimensional stability. The manufacturing process reduces the natural variability and tendency of solid wood to warp, twist, or shrink. This stability makes LVL beams ideal for use in formwork systems, where precise dimensions and reliable performance are paramount.
But what exactly makes LVL beams so strong and stable? It all comes down to the meticulous manufacturing process that goes into creating these remarkable engineered wood products.
The Manufacturing Process of LVL Beams
The manufacturing process of LVL beams involves several steps to ensure their structural strength and durability. It begins with the selection and preparation of high-quality veneer sheets, which are typically made from fast-growing species like pine or eucalyptus. These veneers are carefully inspected for any defects or imperfections that could compromise the integrity of the final product.
Once the veneer sheets pass the rigorous inspection, they are then arranged in a specific pattern, with each layer oriented in the same direction. This strategic orientation of the veneers maximizes the beam’s strength, as it ensures that the grain of each layer runs parallel to the beam’s length.
But it’s not just the arrangement of the veneers that contributes to the strength of LVL beams. The bonding process is equally crucial. Various types of adhesives are used in LVL beam production, including phenol-formaldehyde resin, melamine-urea-formaldehyde resin, and polyurethane resin. These adhesives are carefully selected for their ability to create a strong and durable bond between the veneer layers.
Once the veneer sheets are prepped and the adhesives are applied, the next step is to subject the entire assembly to heat and pressure. This process, known as hot pressing, activates the adhesives and creates a strong bond between the veneer layers. The temperature and pressure levels are carefully controlled to ensure optimal bonding and dimensional stability.
After the hot pressing stage, the LVL beams are trimmed to the desired dimensions and undergo a final inspection to ensure that they meet the required quality standards. This meticulous manufacturing process guarantees that every LVL beam that leaves the production facility is of the highest quality and ready to withstand the demands of various construction applications.
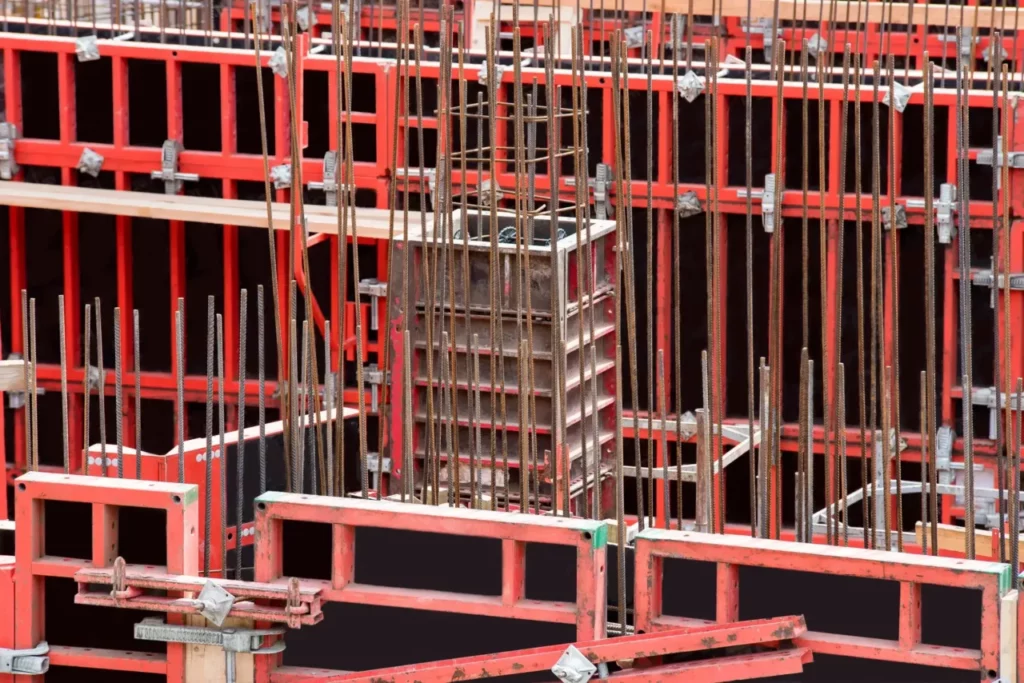
The Role of LVL Beams in Formwork
Importance of LVL Beams in Construction
LVL (Laminated Veneer Lumber) beams are a fundamental component in the construction industry, especially when it comes to formwork structures. These beams are engineered wood products that offer exceptional strength and durability, making them ideal for supporting the weight of concrete during construction projects. Their composition of layers of wood veneers bonded together with adhesives provides a reliable and robust solution for formwork support.
LVL beams are known for their consistent quality and performance, ensuring that formwork systems can maintain stability and integrity throughout the concrete pouring process. Their resistance to warping, twisting, and shrinking makes them a reliable choice for withstanding the pressures exerted by wet concrete and the construction environment.
Additionally, LVL beams are manufactured to precise dimensions, offering uniformity that is essential for achieving accurate formwork alignment and concrete placement. This dimensional accuracy not only enhances the structural integrity of the formwork but also contributes to the overall quality and precision of the construction project.
To read about lvl construction click here.
How LVL Beams Support Formwork Structures
Within formwork systems, LVL beams serve as the backbone that transfers the weight of the concrete to the supporting framework. By evenly distributing the loads, these beams help prevent any potential stress points that could compromise the formwork’s stability. This load-bearing capability is crucial for ensuring the safety and reliability of the formwork structure during the concrete curing process.
Moreover, the versatility of LVL beams allows for easy customization and adaptation to various formwork designs. Whether it involves cutting, shaping, or joining beams together, the flexibility offered by LVL beams enables construction professionals to create intricate and tailored formwork systems that meet specific project requirements. The reusability of LVL beams further adds to their appeal, providing a sustainable and cost-effective solution for multiple construction projects. Read more about reusability on https://www.igi-global.com/dictionary/integrating-simulations-across-a-curriculum/25316
Analyzing the Strength of LVL Beams
Factors Influencing the Strength of LVL Beams
Several factors influence the strength of LVL beams, including the quality of the veneer used, the adhesive type, and the number of veneer layers. High-quality veneers and adhesives result in stronger beams with higher load-carrying capacities.
The orientation of the veneer layers is also critical. By placing the grain orientation parallel to the beam’s length, LVL beams can withstand higher bending and shear forces. Additionally, the uniformity of layer thickness and adhesive distribution contributes to the overall strength of LVL beams.
Furthermore, the manufacturing process plays a crucial role in determining the strength of LVL beams. Factors such as temperature and pressure during the pressing stage, as well as the curing time of the adhesive, impact the final strength and durability of the beams. Manufacturers must carefully control these variables to ensure consistent quality and performance.
Measuring the Strength of LVL Beams
Various testing methods are employed to measure the strength of LVL beams. Bending tests, conducted by applying a load to the center of a supported beam, assess the beam’s resistance to bending forces. Shear tests evaluate the strength of the adhesive bond between the veneer layers.
Other tests, such as modulus of elasticity and modulus of rupture tests, provide insights into the stiffness and breaking point of LVL beams. These tests help manufacturers optimize their production processes and ensure the quality and performance of their LVL beams.
Moreover, non-destructive testing techniques, like ultrasound and x-ray scanning, are increasingly being used to assess the internal structure of LVL beams without causing damage. These advanced methods allow for a more thorough evaluation of the beams’ integrity and can detect any potential defects or weaknesses that may affect their strength and performance over time.
Assessing the Durability of LVL Beams
Factors Affecting the Durability of LVL Beams
The durability of LVL beams depends on various factors, including the type of wood species used for veneers, the adhesive formulation, and the environmental conditions the beams are exposed to. Proper treatment and protection against pests, fungi, and moisture are crucial for enhancing the durability of LVL beams.
Wood species selection plays a significant role in determining the durability of LVL beams. Hardwood species like oak and maple offer higher resistance to decay and insect attacks compared to softwood species such as pine or spruce. The choice of wood veneers can impact the overall strength and longevity of LVL beams, making it essential to consider the specific requirements of the intended application.
Environmental factors, such as temperature fluctuations and ultraviolet (UV) exposure, can also impact the long-term performance of LVL beams. Therefore, careful consideration of these factors during design and construction is essential to ensure the longevity of LVL beam structures.
Longevity and Maintenance of LVL Beams
LVL beams, with their inherent strength and durability, have a long lifespan when properly maintained. Regular inspections, moisture monitoring, and prompt repairs of any damages are essential to ensure the ongoing performance and safety of LVL beam structures. Click here to find more about damages.
Proactive maintenance practices, including the timely replacement of damaged coatings and sealants, can significantly extend the lifespan of LVL beams. Implementing a comprehensive maintenance schedule that includes cleaning, inspection, and repair protocols is crucial for preserving the structural integrity of LVL beam installations over time.
Additionally, proper surface protection, including the application of coatings or sealants, can enhance the resistance of LVL beams to moisture and UV exposure. Following manufacturer guidelines and best practices for storage, handling, and installation will also contribute to the longevity and durability of LVL beams.
Future Developments and Innovations in LVL Beams
Technological Advancements in LVL Beam Production
With advancements in manufacturing technologies, the production of LVL beams continues to evolve. Advanced scanning and optimization systems improve the efficiency and precision of veneer selection and layout, resulting in stronger and more consistent beams.
New adhesive formulations and curing processes are being developed to enhance the bond strength and durability of LVL beams. This ongoing research and innovation aim to further improve the structural properties and overall performance of LVL beams in formwork systems.
One exciting development in LVL beam production is the integration of artificial intelligence (AI) systems. These AI systems analyze vast amounts of data to optimize the manufacturing process, predicting the ideal combination of veneer thickness, adhesive application, and curing time. By harnessing the power of AI, manufacturers can achieve even greater efficiency and precision, leading to LVL beams with unparalleled strength and durability.
Sustainability and LVL Beams in Construction
LVL beams offer significant sustainability benefits compared to other construction materials. Their production utilizes fast-growing wood species, reducing the pressure on old-growth forests. The manufacturing process also minimizes waste, with residual wood chips and veneer trimmings often utilized for energy generation or as raw materials for other products.
Furthermore, the durability and reusability of LVL beams reduce the need for frequent replacements, resulting in lower environmental impacts. The use of LVL beams in formwork systems aligns with the principles of sustainable construction, promoting resource efficiency and reducing carbon emissions.
Looking ahead, researchers are exploring the potential of incorporating recycled materials into LVL beam production. By utilizing recycled wood fibers and adhesives, manufacturers can further reduce the environmental footprint of LVL beams, making them an even more sustainable choice for construction projects.
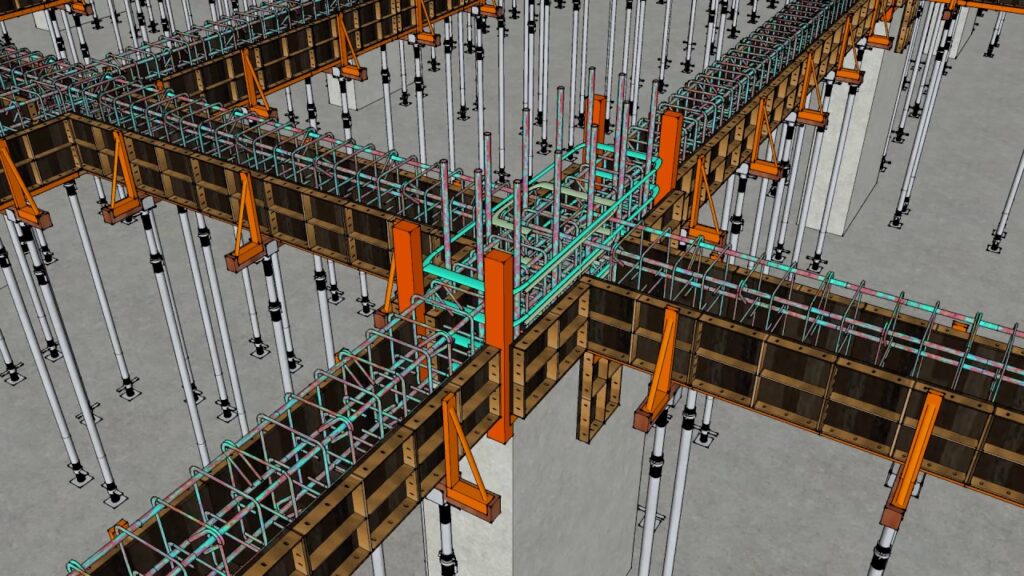
In conclusion, LVL beams are an essential component in formwork systems, providing the necessary strength and durability for construction projects. Understanding the manufacturing process, analyzing the factors influencing strength and durability, and staying informed about advancements in LVL beam production will contribute to optimal utilization of this versatile construction material. With continued research and innovation, LVL beams will continue to play a vital role in the construction industry, supporting sustainable and resilient infrastructure development.
Leave a Reply