Large-scale construction projects require materials that are strong, durable, and cost-effective. One such material that meets these requirements is Laminated Veneer Lumber (LVL). LVL construction materials have gained popularity in recent years due to their unique properties and numerous benefits. This article will explore the significance of LVL materials in large-scale projects, their structural advantages, cost and time efficiency, environmental impact, and future trends in the construction industry.
Understanding LVL Construction Materials
Laminated Veneer Lumber (LVL) is engineered wood made from layers of thin wood veneers glued together with high-strength adhesive. These veneers are typically sourced from fast-growing trees, making LVL a sustainable option for construction projects. The manufacturing process of LVL involves bonded layers that provide enhanced strength and stability compared to traditional solid wood.
One fascinating aspect of LVL construction materials is their versatility in design and application. They can be customized to meet specific project requirements, whether it’s creating curved beams or long-span joists. This adaptability opens up a world of possibilities for architects and builders looking to push the boundaries of structural design.
Definition and Properties of LVL Materials
LVL materials are characterized by their exceptional strength-to-weight ratio. This property makes them ideal for large-scale projects where heavy loads need to be supported. Additionally, LVL materials possess uniformity in strength and dimensions, allowing for predictable performance and ease of use.
Furthermore, LVL materials exhibit excellent resistance to warping, splitting, and bowing, ensuring long-term structural integrity in various environmental conditions. This durability factor makes them a reliable choice for projects requiring robust and long-lasting structural components.
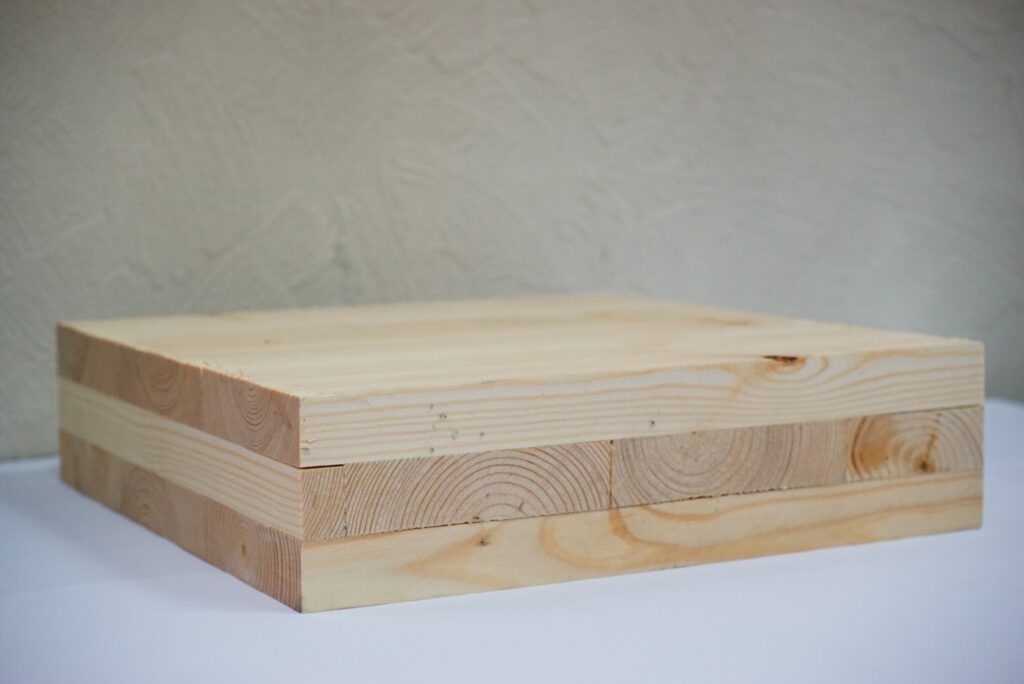
The Manufacturing Process of LVL Materials
During the manufacturing process, the thin wood veneers are carefully selected and arranged in a way that minimizes potential defects. Once arranged, they are bonded together with high-strength adhesive under high pressure and temperature. This process ensures the integrity and durability of the resulting LVL material.
Moreover, the use of advanced technologies, such as computerized scanning and precision cutting, guarantees the consistency and quality of each LVL product. This attention to detail in manufacturing not only enhances the structural performance of LVL materials but also contributes to the overall efficiency of construction processes.
The Role of LVL Materials in Large-Scale Construction
LVL materials play a crucial role in large-scale construction projects due to their structural benefits, cost and time efficiency, and positive impact on the environment.
Structural Benefits of LVL Materials
One of the key advantages of LVL materials is their exceptional strength. They have higher bending and tensile strength compared to traditional solid wood, making them suitable for load-bearing applications. LVL beams and columns can withstand heavy loads, providing structural stability and safety to large-scale projects.
But what sets LVL materials apart is not just their strength, but also their remarkable dimensional stability. Unlike solid wood, LVL materials resist warping and shrinking, ensuring that structures maintain their integrity over time. This characteristic makes LVL a reliable choice for construction projects where stability is crucial.
Imagine a towering skyscraper, standing tall and strong against the forces of nature. LVL materials, with their exceptional strength and dimensional stability, form the backbone of such monumental structures, ensuring their longevity and resilience.
Cost and Time Efficiency of Using LVL
Large-scale construction projects often face tight schedules and budgets. LVL materials offer cost and time efficiency in several ways. Firstly, their uniform strength and dimensions allow for accurate material usage, minimizing waste and reducing overall project costs.
But the benefits of using LVL materials go beyond cost savings. Their lightweight nature makes them easier to handle and install compared to traditional solid wood. Picture a construction site buzzing with activity as workers effortlessly maneuver LVL beams and panels into place, swiftly progressing with the project. This ease of use can lead to faster construction progress, saving time and labor costs.
Moreover, the use of LVL materials aligns with sustainable construction practices. LVL is typically made from fast-growing plantation trees, making it a renewable resource. By choosing LVL, construction projects contribute to the preservation of forests and reduce their carbon footprint. To find more about preservation click here.
So, it’s not just about the immediate cost and time savings, but also the long-term environmental impact that makes LVL materials an attractive choice for large-scale construction projects.
Environmental Impact of LVL Construction Materials
Sustainability Aspects of LVL Materials
LVL materials contribute to sustainable construction practices. They are predominantly made from fast-growing trees, such as pine, that can be harvested and replenished more quickly compared to slow-growing hardwood trees. This renewable source of wood ensures the long-term availability of LVL materials without significant environmental impact.
Furthermore, the production of LVL materials promotes responsible forestry practices. Sustainable forest management techniques, such as selective logging and reforestation programs, are often implemented to ensure the health and biodiversity of the forest ecosystems from which the raw materials are sourced. By supporting these practices, the use of LVL materials helps preserve natural habitats and promotes the overall well-being of forest ecosystems.
LVL Materials and Carbon Footprint
In addition to being renewable, LVL materials have a low carbon footprint. The manufacturing process of LVL requires less energy compared to other building materials, thereby reducing greenhouse gas emissions. Additionally, the use of LVL in construction projects can facilitate energy-efficient designs by providing better insulation and thermal performance.
Moreover, the durability and strength of LVL materials contribute to the longevity of structures, reducing the need for frequent replacements and repairs. This extended lifespan further enhances the environmental benefits of LVL construction materials by minimizing waste generation and resource consumption over time. By choosing LVL materials, builders and designers can support sustainable practices while creating resilient and eco-friendly structures for the future. Learn more about waste on https://www.avma.org/resources-tools/one-health/waste-disposal-veterinary-practices/definitions-what-waste
Future Trends in LVL Construction Materials
Technological Advancements and LVL Materials
The construction industry is constantly evolving, and LVL materials are not exempt from technological advancements. As new manufacturing techniques and adhesive technologies emerge, the quality and performance of LVL materials are expected to improve further. Advanced production methods may enhance the strength, durability, and fire resistance properties of LVL, making it even more desirable for large-scale construction projects.
One exciting technological advancement in the realm of LVL materials is the development of smart LVL, which incorporates sensors to monitor structural integrity and performance in real-time. This innovation not only enhances the safety and reliability of LVL structures but also opens up possibilities for predictive maintenance and data-driven decision-making in construction projects.
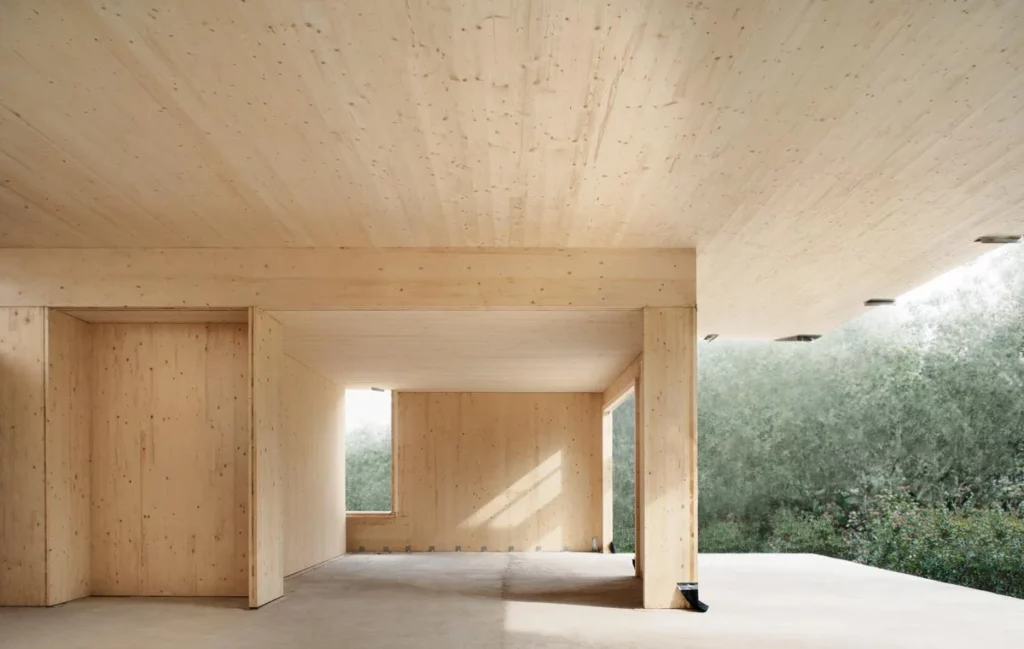
Market Predictions for LVL Materials in Construction
The demand for sustainable construction materials is on the rise, and LVL materials are well-positioned to meet this demand. As awareness and regulations regarding environmental impact continue to grow, the construction industry is likely to embrace LVL materials as a sustainable and cost-effective alternative to traditional wood and concrete.
Furthermore, the versatility of LVL materials allows for innovative design possibilities, enabling architects and engineers to create unique and aesthetically pleasing structures. From curved beams to intricate facades, LVL offers a wide range of design options that can enhance the visual appeal of any construction project.
In conclusion, LVL construction materials are essential for large-scale projects due to their exceptional strength, dimensional stability, cost and time efficiency, and positive environmental impact. As the construction industry moves towards more sustainable practices, the demand for LVL materials is expected to increase. With ongoing technological advancements, LVL is likely to become an even more important player in the future of construction materials.
Read about lvl timber prices on: Tips for Finding the Best LVL Timber Prices for Your Construction Project